Circuits
31 Manual Circuits
A manual circuit is one that is stopped and started by a person. These circuits might have automatic features (such as overload protection) but their main feature is that they require some sort of input from a human operator.
The most fundamental manual circuit is the stop-start three-wire circuit. A firm understanding of this circuit is necessary because many of the features of the three-wire circuit scale upwards to more complex circuits.
Basic Three-Wire Circuit
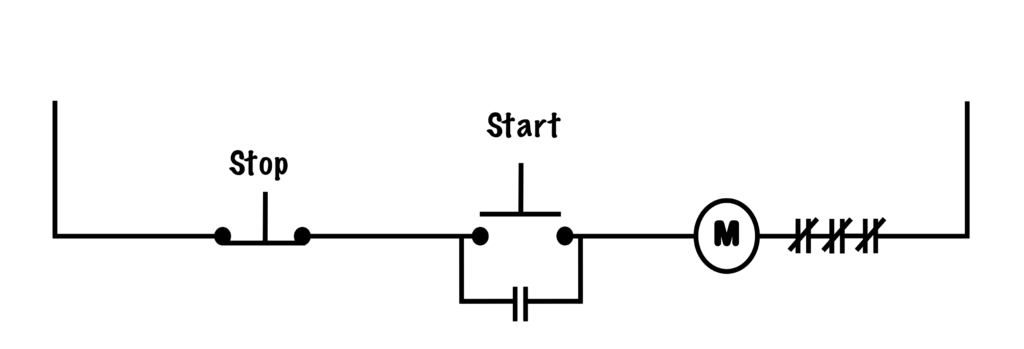
The components in the circuit above consist of a normally closed, momentary-contact stop pushbutton; a normally open, momentary-contact start pushbutton; and a motor starter. These components may be housed in the same compartment, or the pushbuttons could be installed separately from the motor starter. The motor starter itself is connected in series with the three normally closed overload relay contacts.
The unique component of the circuit, indeed the device that allows the circuit to provide low-voltage protection (LVP), is the normally open instantaneous contact connected in parallel with the start button. The normally closed stop button offers no opposition to the flow of current.
When power is on and the motor is not running, current can pass neither the normally open start button, nor the normally open contact, and so the motor does not start.
When an operator comes and pushes the start button, current is able to pass through the contacts as the button is depressed. This completes the circuit and energizes the coil of the motor starter, pulling in the armature. The three horsepower-rated contacts will close, as well as the normally open auxiliary contact in parallel with the start button.
The normally closed contacts in series with the coil are controlled by the thermal action of the overload relays, and not the movement of the armature, so they remain closed as long as an overload does not occur.
Once the normally open contact (called a holding, maintaining or 2 – 3 contact) is closed, the operator is now free to release the start button. The current will continue to have a path through the circuit, keeping the starter coil energized. In reality this all happens in a fraction of a second, and so the holding contact will be closed before the operator’s finger has come off the start button.
Now the motor will continue to run until current to the motor starter is interrupted. This could happen if the operator presses the normally closed stop button or if an overload occurs and one of the normally closed OLR contacts opens up. If a power outage occurs during normal operation, the starter coil will drop out and the motor will stop as well.
In any situation where the motor starter becomes de-energized and the armature is pushed open by the spring inside it, all contacts associated with the coil return to their normal condition. The motor will not restart without further input from an operator as the holding contact will have returned to its normally open state.
With the installation of an auxiliary contact in parallel with the momentary start button, any circuit can provide low-voltage protection (LVP).
https://video.bccampus.ca/id/0_un60v25l?width=608&height=402&playerId=23448552
In motor control terminology, a three-wire circuit utilizes a magnetic motor starter with a holding contact, along with momentary contact pushbuttons. A three-wire circuit provides low-voltage-protection.
A contact that under normal conditions has continuity through it. When the contact changes its state it interrupts the flow of current by opening its contacts. Can be associated with pushbuttons, pilot devices or magnetic contactors.
A momentary contact device that has a built in spring to return the button to its normal position once release. Available with either normally-open, normally-closed or both sets of contacts.
A contact that under normal conditions does not have continuity through it. When the contact changes its state it permits the flow of current by closing its contacts. Can be associated with pushbuttons, pilot devices or magnetic contactors.
A device that controls the flow of electrical power to a motor. It is designed to safely start and stop a motor, and provide overload protection.
In electrical terms, refers to a connection where current has only one path to flow.
Loads connected in series will have the the same value of current flowing through them, and share the total voltage between them. Switches and overcurrent equipment is connected in series with equipment to control and protect it.
A heater element paired with normally-closed contacts that open once the heater gets too hot. Two types of relays are the bimetallic strip and the melting solder pot.
Circuits with low-voltage protection will not automatically turn back on when voltage is restored following a power outage. Examples include the microwave or power tools.
In electrical terms, refers to a connection where current has more than one path to flow.
Loads connected in parallel will experience the same potential difference (voltage), but may draw different values of current depending upon their individual resistance.
The conducting part of a switch that makes or breaks a circuit.
With respect to magnetic contactors, the armature or plunger is the movable part of the magnetic circuit. When a coil is energized the armature is pulled in, opening and/or closing a set or sets of contacts.
A set of contacts that has been designed to make or break the flow of current to a motor and can handle loads up to a specified amount of horsepower at a specific voltage. The size of contacts are determined by the size of the motor they are controlling.
Contacts on a magnetic starter that are not Horsepower rated. Can come as either normally-open or normally-closed and can be used as maintaining contacts, electrical interlocks or control for pilot lights.
A moderate and gradual rise in the value of current over a relatively long period of time that is caused by excessive amounts of current drawn by a motor due to too much load being put on the motor.