5.2 Tools and Techniques for Planning and Controlling Quality of Projects
Several different tools and techniques are available for planning and controlling the quality of a project. The extent to which these tools are used is determined by the project complexity and the organization’s quality management program.
The following represents some of the quality planning tools in use today:
- Cost-benefit analysis looks at how much the quality activities will cost versus how much will be gained from doing them. Typical cost considerations include the effort and resources required to carry out the quality activities. Typical benefit considerations include greater user satisfaction, less reworking, and greater productivity.
- Benchmarking is using the results of quality planning from other projects to set goals for the current project. If the last project in the organization had 20% fewer defects than the one before it, the project team should learn from a project like that and put in practice any of the ideas the previous project used to make such a great improvement. Benchmarks can serve as reference points for evaluating a project before the work begins.
- Design of experiments is the list of the array of tests to be run on the product. It might list all the kinds of test procedures, the approaches to be taken, and even the tests themselves. (In the software world, this is called test planning.)
- Cost of quality is obtained by adding up the cost of all the prevention and inspection activities to be performed on the project. This includes many different activities, such as testing, time spent writing standards, reviewing documents, meeting to analyze the root causes of defects, and reworking to fix defects identified by the team… in other words, absolutely everything that is done to ensure quality on the project. The cost of quality can be compared from one project to another to identify innovative ideas and best practices. The cost of quality model identifies four categories of cost associated with quality. Think of some examples of each:
- Prevention: Prevention costs are incurred to keep defects and failures out of a product. They are planned and incurred before actual operations. E.g. Quality Assurance
- Appraisal: Appraisal costs are associated with measuring and monitoring activities related to quality. E.g. Quality audits
- Internal Failure: Internal failure costs are associated with finding and correcting defects before the customer receives the product. E.g. Wastes
- External Failure: External failure costs are associated with defects found after the customer has the product and with remediation. E.g. Warranty claims
- Control charts can be used to define acceptable limits. If some of the functions of a project are repetitive, statistical process controls can be used to identify trends and keep the processes within control limits. Part of the planning for controlling the quality of repetitive processes is to determine what the control limits are and how the process will be sampled.
- Cause-and-effect diagrams can help in discovering problems. When control charts indicate an assignable cause for a variation, it is not always easy to identify the cause of a problem. Discussions intended to discover the cause can be facilitated using a cause-and-effect, or fishbone diagram, where participants are encouraged to identify possible causes of a defect.
Example: Diagramming Quality Problems
A small manufacturing firm tries to identify the assignable causes of variations in its manufacturing line. They assemble a team that identifies six possibilities:
- Low-quality raw materials
- Power fluctuation
- Ambient temperature
- Worker absenteeism
- Poor training
- Old equipment
Each of these possibilities is organized into a fishbone diagram below.
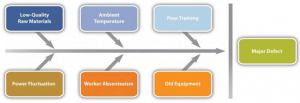
Then, each branch of the diagram can be expanded to break down a category into more specific causes. An engineer and an electrician work on one of the branches to consider possible causes of power fluctuation. They identify:
- Utility reliability
- Personal space heaters and large motor start-up leading to overloaded circuits
- Lighting
Those items are added to their part of the fishbone diagram, as shown below.
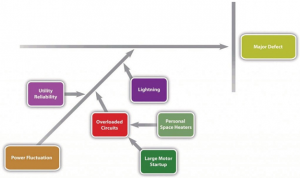
Check sheets, histograms, and Pareto charts are also used to solve several quality problems. When a quality-control issue occurs, a project leader must choose which problem to address first. One way to prioritize quality problems is to determine which ones occur most frequently. These data can be collected using a check sheet, a basic form on which the user can check in the appropriate box each time a problem occurs, or by automating the data collection process using the appropriate technology.
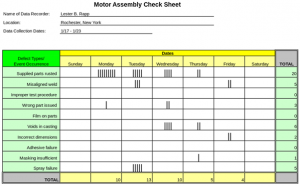
Once the data are collected, they can be analyzed by creating a type of frequency distribution chart called a histogram. A true histogram is a column chart where the widths of the columns fill the available space on the x-axis axis and are proportional to the category values displayed on that axis, while the height of the columns is proportional to the frequency of occurrences. Most histograms use one column width to represent a category, while the vertical axis represents the frequency of occurrences.
A variation on the histogram is a frequency distribution chart invented by economist Vilfredo Pareto known as a Pareto chart. The columns are arranged in decreasing order, with the most common on the left and a line added that shows the cumulative total. The combination of columns and a line allows the user to tell at a glance which problems are most frequent and what fraction of the total they represent. For instance, in Exhibit 5.4, there are six reasons why travelers arrive late at the airport. Traffic is the number one reason, and 55 participants reported it. Approximately 154 people participated in this study.
Traffic represents approximately 36% of the total late arrivals (55/154). The second highest cause, child care issues, represents 26% of the total. Cumulatively, traffic and child care issues represent 62% of the total. The third cause, public transportation issues brings the cumulative total to approximately 80% of the total. Understanding what causes the majority of the issues allows a team to prioritize and focus on these key factors. In this case, if the airport wanted to reduce the number of late arrivals, they could focus on traffic, childcare, and public transportation issues.

Other tools include:
- Surveys and Questionnaires
- Meetings
- Brainstorming
- Affinity diagrams
- Nominal group techniques
- Matrix diagrams
- Prioritization matrices
- Force field analysis