7 Tooling
Jointers are capable of producing an extremely smooth, clean cut if the tooling is kept sharp and free of nicks. If the machine seems to not be cutting properly, for example the cut seems to taper slightly, or it is difficult to get two pieces cleanly edge jointed for glue-up, it may be time to change the tooling. Tracks on the surface indicate nicks in the knives, however it is not always possible nor desirable to change knives for every nick. The fence can be positioned to avoid them, especially for narrow pieces. The knives can also be laterally offset from each other a small amount by loosening the gibs and repositioning them. This ensures that the nick on each knife is in a different spot, the other knives will then remove the track left by the damaged knife.
To keep the tooling sharp and in good condition for as long as possible, observe these guidelines:
- Never place material to be machined on the floor. It will pick up grit that will dull and damage the cutters.
- Never joint plywood or composites such as MDF, or painted or finished wood.
- Trim the raw ends of boards before jointing. They often have metal staples from inventory tags. The ends of logs are usually sealed at the mill to help prevent drying defects, the sealer is abrasive and will prematurely wear the cutter.
- Inspect the edges of every board for staples.
There are three types of tooling commonly used for jointers, including straight knives, disposable, and carbide insert.
Standard straight knives
Straight knives are commonly found on many jointers, both smaller models and larger industrial machines. In recent years, helical cutterheads have begun to replace straight knives on higher end tools.
The knives are often available in either high speed steel (HSS) or carbide tipped. HSS is a good choice for most work, and will produce an excellent surface quality. Carbide tipped knives cost quite a bit more in comparison, but will last longer before requiring sharpening. They are recommended for use in production settings, and for used with extremely hard and abrasive woods.
HSS knives can be honed in the shop with regular sharpening stones. Care must be taken to keep the entire edge of the knife perfectly straight, and to prevent rounding over of the cutting edge. To achieve this, the knives can be honed while in position in the cutterhead. A strong paper or plastic can be wrapped around part of the stone to prevent it from cutting into the outfeed table. The cutterhead is rotated until the knife edge is horizontal but a little higher at the toe. The outfeed table may have to be adjusted to accommodate this. The cutterhead is then wedged in position and the knife edges honed in turn. Once the bevel is honed, a slip stone may be used to remove the wire edge. If using water stones, ensure no excess moisture may wick between the knife and the cutterhead where corrosion could occur.
While HSS can be touched up with sharpening stones, both HSS and carbide knives are commonly sent out of shop a service to be precision ground and sharpened. The knives must be balanced, or the same weight as each other, to reduce vibration. Both types can be sharpened many times before they must eventually be replaced.
Indexing, disposable
Because multiple knives must be installed in perfect alignment, manufactures have developed knives that have a way of perfectly indexing with the cutterhead, negating the need for manual alignment. They are quick and easy to install. Some jointers and most portable planers use this type of knife. Many types of these knives are double sided and may be rotated once for a new, sharp edge. All of the indexing knives are disposable.
Different means of locating or indexing the knives have been developed. Some use a simple pin and hole method, where the knife has a hole that indexes to a pin on the cutterhead. Machine screws then secure the knife to the cutterhead. Another system is Tersa™ knives. These are double sided, and instead of being flat have an indent on the face that meets the cutterhead. A wedge is then inserted to keep the knife in place. Centrifugal force acts on the knife and wedge when the machine is running to lock everything in place, negating the need to use any fasteners.
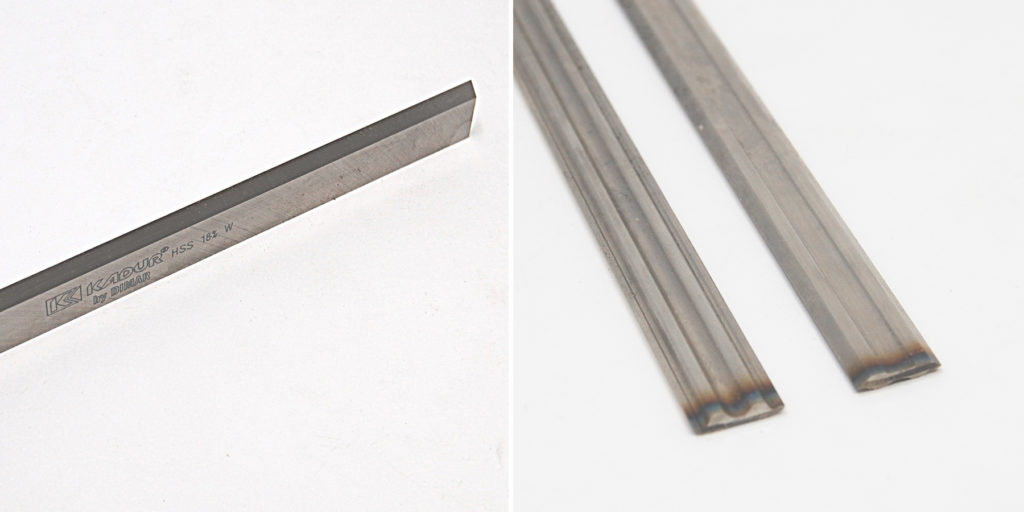
Helical
A different type of cutterhead is now found on many jointers and planers. It uses a completely different system, replacing the typical three of four straight knives with a series of small carbide cutters. These cutters are arranged in a helical shape. This shape creates a shearing cutting action that slices the wood fibres more cleanly. Tooling that makes use of disposable carbide cutters that index to the tool body is known as insert tooling.
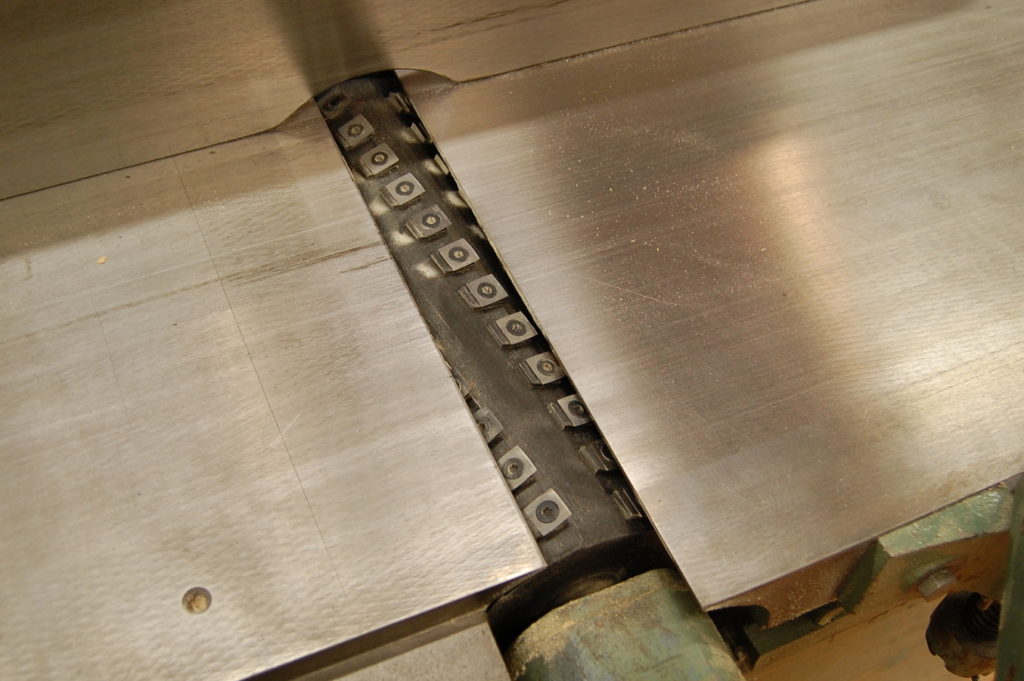
The carbide cutters are small squares that have a slightly radiused edge, which also contributes to the shearing action of the cutter. The cutters are disposable, however they may be rotated to use all four edges before needing to be replaced. Because the cutters are staggered in their rows, if a small rock or staple is run into the machine, usually only one or two cutters are damaged. When a cutter is damaged, it may be rotated for a fresh edge. In a straight knife cutterhead, the entire knife or set must be removed for sharpening if damage occurs. The cutters are secured to the cutterhead with machine screws. The shearing action of a helical cutterhead has a great advantage in the machining of figured woods as tear-out is greatly reduced. They also run quieter compared to straight knife cutterheads.
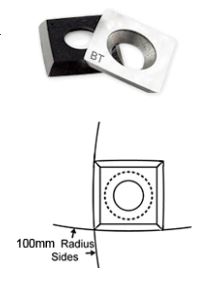