12 Use of the Planer
Safety rules
As the cutterhead in a planer is completely enclosed and the machine feeds the stock rather than the operator, the planer has less potential for accidents than many other woodworking machines. However, there is still potential for injury. Follow these safety rules for the planer.
- The shortest length the planer can accommodate is the distance between the center of the infeed and outfeed rollers plus 50 mm / 2″. This ensures at least one feed roller is securing the stock.
- Never place your hands into the machine unless the power supply is locked out.
- A pinch hazard exists between the stock being planed and the table. Ensure your fingers and hands are never between the stock and the bed.
- When planing short stock or planing a heavy pass, the infeed rollers can cause the workpiece to tilt up and then slam down as it engages. Ensure your hands are never under the workpiece at any time.
- As the planer is self feeding, anything that engages with the material being fed will be pulled in to the machine. Be aware of loose clothing or jewelry.
- Stand to the side of the planer on the infeed side to avoid a potential kickback.
- Do not stand between the out feeding stock and anything solid such as a wall or other machine as you could be pinched.
- Small pieces, especially knots may break off in the planer and be ejected toward the operator.
- Follow all general machine safety rules.
Stock preparation
The minimum length of stock that can be fed through the planer is equal to the distance from centre to centre between the infeed and outfeed rollers, plus about 50 mm / 2″. This ensures the material being passed through the machine is always being held by one roller. If shorter parts are to be machined, leave them in multiple lengths for jointing and planing, then crosscut them to size after. This method ensures the parts can be safely machined, and also decreases parts handling.
Material that is to be planed should be inspected for grit, staples or any foreign material that could damage the tooling. Never place stock on the floor where it can pick up grit and small particles that will dull and damage the tooling. Material to be planed should first be jointed to remove any bow, twist or cup.
Before turning on the machine, organize all the parts to ensure they have the jointed face down, and the grain is running in the correct direction to prevent tear out. The cutterhead turns opposite to feed direction. The grain should slope downward toward the end that will be fed in the planer.
Never plane plywood or composites such as MDF, or painted or finished wood, and never place material to be machined on the floor. It will pick up grit that will dull and damage the cutters.
Depth of cut
Check the pieces to be planed at both ends and the middle to determine the thickest dimension. Set the planer to remove an amount appropriate to this thickness. If the planer is not set for the thickest piece, often it will not pass into the planer and the table must be lowered to catch it up.
It is often necessary to take multiple passes through the planer to achieve the desired depth of cut.
Typically, a stationary planer can remove about 2 mm (1/16″) to 4 mm (1/8″) in a single pass. Large industrial planers can usually remove more. Small portable planers should not remove more that 2 mm (1/16″) per pass. Volume of cut is also a factor, using the entire length of the cutterhead when planing wide panels usually necessitates reducing the amount of material removed in a single pass. The best way to determine if the depth of cut is too heavy is to listen to the machine, if it is excessively noisy or is bogging down, reduce the depth of cut.
Planing multiple parts to a common size
When multiple parts are to be machined to a common size, it is important that all parts are run through the planer at the same depth setting for accuracy. It is difficult to reset the planer to cut exactly the same thickness. When multiple passes are required, plane all the pieces at the same setting before advancing the depth of cut.
Removing large amounts of material
When reducing stock significantly in thickness, run pieces through until they all have a clean side and are the same thickness. Then alternate surfaces with each pass until the desired thickness is achieved. This reduces the chance of warping as potential tension in the piece is released and the moisture content equalizes.
Orientation of stock
The majority of planing operations involve face planing. This is the most stable arrangement as the stock can’t tip over. It is acceptable to plane stock on edge as long as it is stable. Wide, thin pieces should be avoided. Whenever possible, multiple pieces should be placed face to face before being run through on edge to increase stability.
Reducing snipe
Snipe occurs when the ends of the piece being planed lift up slightly into the cutterhead and are cut beyond the desired depth. It occurs at the ends when the piece is held by only one roller. The height of the bed or idler rollers can increase the amount of snipe if they are set too high. With many planers, a small amount of snipe is unavoidable.
Running the stock with the ends butted tightly together can decrease the amount of snipe and is good practice when planing multiple parts. It is also good practice to vary the position of the stock in the planer to use the entire width of the cutting head so the tooling wears evenly. A backer board can also be useful in reducing snipe as it isolates the idler rollers. Ensure it has a smooth surface to reduce friction.
Planing thin stock
The planer has a stop that prevents the cutterhead from contacting the table. The minimum thickness that can be planed varies depending on the machine. Be aware that the thinner the stock is planed, the less integrity is inherent in the material. Very thin stock has a tendency to break apart when planing, especially if there is any grain runout. When material less than 12 mm or 1/2″ is to be planed, a backer board of MDF or other dense composite material is recommended. They ensure smooth feeding of the material, and reduce the chance of the thin stock deflecting on the bed rollers.
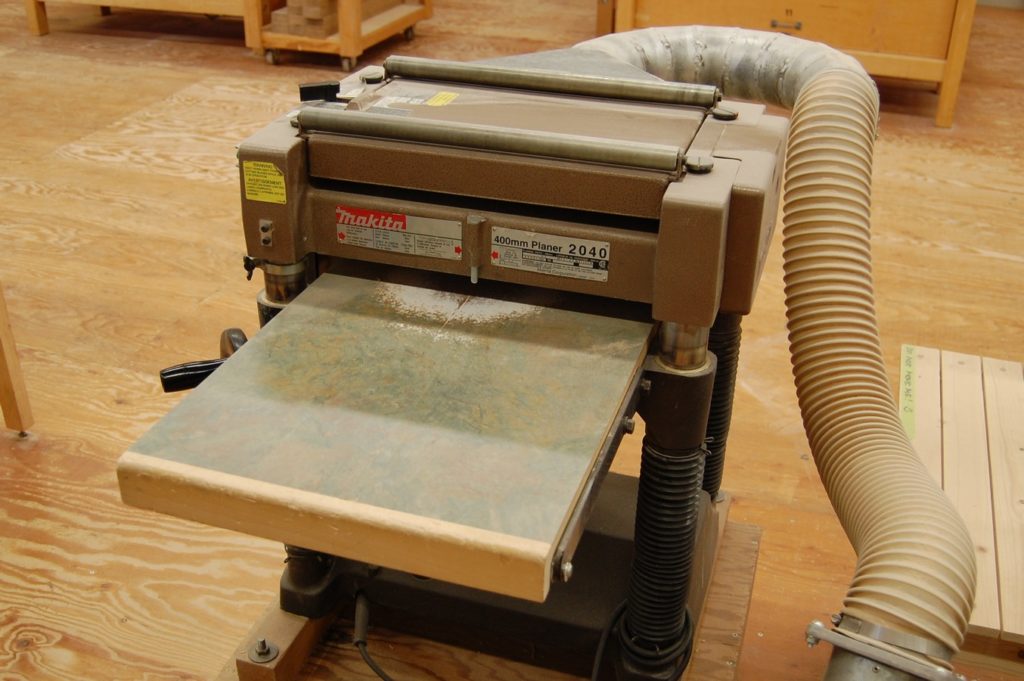